开炼机总体介绍
开炼机是开放式炼胶机的简称,在橡胶、塑料加工等领域有着广泛的应用。它主要由两异向向内旋转的中空辊筒或钻孔辊筒组成,其中前辊可通过手动或电动方式水平前后移动以调节辊距,适应不同的操作要求,后辊则是固定的。两辊筒大小一般相同,以不同速度相对回转,生胶或胶料随着辊筒的转动被卷入两辊间隙,在强烈剪切作用下达到塑炼或混炼的目的。
在塑料制品生产中,开炼机被广泛应用于混炼、塑化等操作。例如,在压延机生产线上,开炼机位于压延机前、混合机后,其作用是将混合均匀的原料进行混炼、塑化,为压延机压延成型塑料制品提供混合炼塑较均匀的熔融料。在生产电缆料时,开炼机能直接把按配方混合好的粉状料炼塑成熔融料,再压塑成片状带,便于切粒机切成粒状。在地板革生产线上,开炼机可直接为布基革提供混炼塑化均匀的底层涂料。同时,还可把回收的废旧塑料薄膜(片)在开炼机上重新炼塑回制。
开炼机结构简单,制造比较容易,操作也容易掌握,维修拆卸方便,因此在塑料制品企业广泛应用。然而,其也存在不足之处,工人操作时体力消耗很大,在较高温度环境中需要用手工混炼翻动混炼料,而手工翻转混炼塑料片的次数多少对原料混炼的质量影响较大。
二、开炼机的工作原理
原理阐述
开炼机的工作原理主要是通过两个相对回转的辊筒对胶料产生剪切、挤压作用。具体来说,用开炼机进行塑炼时,两个辊筒的相对回转会对胶料施加作用力,使胶料原有的大分子链被打断。这一过程就如同将原本坚韧的绳索剪断成较短的片段,从而使得胶料原有的弹性降低,可塑度提高,有利于后续加工工序的进行。目前使用的塑炼方法主要是包辊塑炼法和薄通塑炼法。
在炼胶过程中,开炼机主要依靠两个相对回转的辊筒对胶料产生挤压、剪切作用,经过多次捏炼,以及捏炼过程中伴随的化学作用,将橡胶内部的大分子链打断,使配方中的各种成分掺和均匀,最终达到炼胶的目的。从辊筒间隙中排出的胶片,由于两个辊筒表面速度和温度的差异而包覆在一个辊筒上,重新返回两辊间,这样多次往复,完成炼胶作用。在塑炼时促使橡胶的分子链由长变短,弹性由大变小;在混炼时促使胶料各组分表面不断更新,均匀混合。
在间歇操作的开炼机上,加料后胶料反复通过辊距数次,最后切割下片。而在用作连续操作的开炼机上,胶料从辊筒的一端连续加入,按炼胶工艺规定的时间反复通过辊筒数次,从辊筒的另一端连续切割所要求的胶条。
开炼机混炼的工作原理是利用两个平行排列的中空辊筒,以不同的线速度相对回转,加胶包辊后,在辊距上方留有一定量的堆积胶。堆积胶拥挤、绉塞产生许多缝隙,配合剂颗粒进入到缝隙中,被橡胶包住,形成配合剂团块。随胶料一起通过辊距时,由于辊筒线速度不同产生速度梯度,形成剪切力。橡胶分子链在剪切力的作用下被拉伸,产生弹性变形,同时配合剂团块也会受到剪切力作用而破碎成小团块。胶料通过辊距后,由于流道变宽,被拉伸的橡胶分子链恢复卷曲状态,将破碎的配合剂团块包住,使配合剂团块稳定在破碎的状态,配合剂团块变小。胶料再次通过辊距时,配合剂团块进一步减小,胶料多次通过辊距后,配合剂在胶料中逐渐分散开来。采取左右割刀、薄通、打三角包等翻胶操作,配合剂在胶料中进一步分布均匀,从而制得配合剂分散均匀并达一定分散度的混炼胶。
三、开炼机的主要组成部分
辊筒
辊筒是开炼机的主要工作部件,在工作过程中,它直接与胶料接触,对胶料产生挤压和剪切作用。双棍开炼机利用不同转速相对运动的两个辊产生剪切力来塑炼,操作过程中要不断对胶料进行打三角包或卷曲等操作。
辊筒需要具有一定的机械强度、刚度,能承受胶料的作用力;工作表面要有较高的耐磨性和耐腐蚀性,且表面硬度不低于肖氏 65°;具有合理的几何形状,防止应力过度集中;具有较好的导热性能,便于胶料的加热和冷却;制造工艺简单、造价低;直径误差为 1~0.5mm,表面粗糙度为 3.2~1.6,出厂检验一定要保证辊径有正的偏差。
辊筒材料一般为冷硬铸铁,实验用的小型开炼机辊筒也采用中碳合金钢。
轴承
开炼机的滚子轴承主要有两种结构形式:滑动轴承和滚动轴承。
滑动轴承是开式磨机常用的滚子轴承类型,结构简单,制造方便,成本低。润滑剂为干黄油或稀机油。轴承体材料用铸铁或铸钢制造,其抗拉强度不低于 200Mpa,一般用 HT200 铸铁;轴衬用金属(青铜)或非金属(MC 尼龙)制造,尼龙轴衬的缺点是导热性能差,热膨胀大。
滚动轴承具有使用寿命长、摩擦损失小、节能、安装方便、维修方便等特点,但造价高,配套困难,使用较少。
机架
机架为开炼机提供稳定的支撑结构,确保开炼机在工作过程中保持稳定。
压盖
压盖起到一定的保护和固定作用,防止胶料在加工过程中飞溅,同时也对其他部件起到一定的固定作用。
传动装置
传动装置驱动辊筒转动,常见的传动形式有开式传动、闭式传动、双电机驱动、组合驱动、整体式、角式传动和液压驱动等。
开式传动由主电机通过减速器带动驱动齿轮和一对速比齿轮驱动前、后辊筒,两辊筒以不同的线速度相对回转。闭式传动是将全部的传动齿轮集中在一个减速箱体内,前、后辊筒由主电机通过闭式传动减速器和万向联轴器驱动。双电机驱动动力由两台电机分别驱动闭式减速器中的两组减速齿轮,减速后经万向联轴器带动前、后辊筒转动。组合驱动是用一台减速器同时驱动两台或多台开炼机的机体部分。整体式开炼机动力由置于辊筒下方的电机和装在机架内腔的齿轮减速后,传递到驱动大、小齿轮和速比齿轮,带动前、后辊筒转动。角式传动由电机带动圆锥齿轮减速器和大、小驱动齿轮及速比齿轮,从而驱动前、后辊筒。液压驱动以液压马达作为动力来源,在机体的两侧,前、后辊筒的端部各安装一套液压马达,单独对每个辊筒进行驱动。
调距装置
调距装置可调整辊筒间距,适应不同的操作要求。常见的调距装置有手动调距装置、电动调距装置、液压调距装置。
调整辊距的步骤如下:确保开炼机已停机且电源已切断。根据生产工艺要求,测量或查看上下辊之间的距离。如果需要调整,使用手工调节装置进行调整。将等效线速度调整到标准值,并开启调节装置的动力源。从进料端开始逐组调节辊距,放松调节螺母,逐一调整辊窑宽度,并在调整完成后紧固螺母。调节完成后,启动开炼机,向进料端投料,观察生产过程中的工艺指标变化。若发现不良生产指标,需重新校准辊距。最后,锁紧上辊和下辊的锁紧螺母,确保辊距不再发生变化。然后启动开炼机进行测试运行,观察是否正常运转,是否存在异常情况。注意安全,并在整个过程中监控设备的运行状态。
润滑装置
润滑装置保证设备的正常运转,减少磨损。开炼机辊筒轴承所承担的负荷很大,且滑动速度低,温度较高。因此,要求轴承耐磨、承载能力强、使用寿命长、制造及安装方便。滑动轴承的润滑剂为干黄油或稀机油,滚动轴承润滑油消耗量与一般滑动轴承相比可减少 75%。
辊温调节装置
辊温调节装置控制辊筒温度,满足不同工艺需求。滚筒温度调节装置有开式和闭式两种。开放式结构简单,散热效果好,水温可以用手检测和测量,水管堵塞也很容易发现等特点,缺点是冷却水消耗量大。封闭式冷却效果不理想,但结构紧凑,冷却水消耗量小。
紧急停车装置及制动装置
紧急停车装置及制动装置确保操作安全,在紧急情况下能迅速停止设备。常见的安全装置有拉杆式安全门、紧急停车开关、限位开关、安全防护罩等。拉杆式安全门通过拉杆的固定与炼机框架相连,当门打开时会自动切断电源。紧急停车开关是一种通过触发开关实现炼机紧急停车的安全装置。限位开关是一种通过限制操作部件运动范围实现炼机安全控制的装置。安全防护罩是一种通过物理隔离实现机器运转时,可以防止操作人员意外触碰到炼机框架或滚筒等的装置。
四、开炼机的优缺点
优点
开炼机具有诸多优点,使其在橡胶、塑料加工等领域仍占有一席之地。
首先,结构简单,制造比较容易。相比一些复杂的机械设备,开炼机的设计和制造过程相对简便,不需要过高的技术要求和复杂的工艺,这使得其生产成本相对较低,也便于生产厂家进行大规模生产。
其次,操作也容易掌握。对于操作人员来说,不需要经过长时间的专业培训就能熟练掌握开炼机的操作方法,降低了企业对员工培训的成本和时间投入。而且,维修拆卸方便,当设备出现故障时,维修人员可以快速地对设备进行拆卸和维修,减少了设备停机时间,提高了生产效率。
再者,塑化条件调节容易。操作人员可以根据不同的原料和生产要求,灵活地调整开炼机的各项参数,如辊距、辊速、温度等,以达到最佳的塑化效果。同时,生产能力大,出料规则,能够满足大规模生产的需求。
此外,散热快,不易死料。开炼机的开放式结构使得胶料在加工过程中能够快速散热,避免了因温度过高而导致胶料变质或烧焦的情况发生。而且,即使在长时间的运行过程中,也不容易出现死料现象,保证了生产的连续性和稳定性。
最后,可以点动反转,操作灵活。这一特点使得操作人员在处理一些特殊情况时更加方便,能够及时调整胶料的位置和状态,提高了生产的可控性。
同时,传动部分扭力大,下料多。这使得开炼机在处理一些较硬的原料或大量的原料时也能轻松应对,提高了生产效率。
缺点
然而,开炼机也存在一些明显的缺点。
其一,工人操作体力消耗很大,劳动强度高。在开炼机的操作过程中,工人需要频繁地进行手工混炼翻动混炼料,尤其是在较高温度的环境下,这不仅需要耗费大量的体力,还容易导致工人疲劳和受伤。
其二,每个批次因素不同,炼出来的胶不稳定。由于开炼机的操作过程中受到多种因素的影响,如工人的操作手法、原料的质量、温度、湿度等,使得每个批次生产出来的胶料质量存在一定的差异,难以保证产品的稳定性。
其三,不安全,裸露在外面。开炼机的开放式结构使得操作人员在操作过程中容易接触到高速旋转的辊筒等部件,存在较大的安全隐患,容易发生工伤事故。
其四,混炼量少,产能低。与一些先进的混炼设备相比,开炼机的混炼量相对较少,这限制了其在大规模生产中的应用,导致产能较低。
其五,不易散热。虽然开炼机在某些情况下散热快,但在一些特殊的生产工艺中,也可能出现不易散热的情况,这会影响胶料的质量和生产效率。
五、开炼机的应用领域
橡胶工业
开炼机在橡胶工业中有着至关重要的作用。它主要用于橡胶的塑炼、混炼、热炼、压片和供胶。在塑炼过程中,开炼机的两个辊筒相对回转,对胶料施加作用力,将橡胶内部的大分子链打断,使橡胶的弹性降低,可塑度提高,为后续的加工工序做好准备。在混炼时,开炼机能促使胶料各组分表面不断更新,均匀混合,使配方中的各种成分掺和均匀。热炼过程中,开炼机通过对胶料的反复挤压和剪切,使胶料温度升高,达到合适的加工温度。压片操作则是将胶料压制成片状,方便后续的加工和使用。此外,开炼机还可用于再生胶片生产中的粉碎、捏炼和精炼,使废旧橡胶得到再利用,减少资源浪费。
塑料加工
在塑料制品生产中,开炼机主要进行混炼、塑化等操作,为压延机提供混合炼塑较均匀的熔融料。位于压延机前、混合机后的开炼机,将混合均匀的原料进行混炼、塑化,确保为压延机压延成型塑料制品提供高质量的熔融料。例如在生产电缆料时,开炼机能直接把按配方混合好的粉状料炼塑成熔融料,再压塑成片状带,便于切粒机切成粒状。在地板革生产线上,开炼机可直接为布基革提供混炼塑化均匀的底层涂料。同时,还可把回收的废旧塑料薄膜(片)在开炼机上重新炼塑回制,实现资源的循环利用。
其他行业
开炼机广泛应用于油漆颜料、电线电缆、建材等行业的生产中。在油漆颜料行业,开炼机可以将各种颜料和添加剂充分混合,提高颜料的质量和稳定性。在电线电缆行业,开炼机能够将橡胶或塑料原料与各种助剂混合均匀,为电线电缆的绝缘层和护套层提供优质的材料。在建材行业,开炼机可以用于生产各种塑料建材,如塑料管材、板材等,提高建材的性能和质量。
六、开炼机的安全操作与注意事项
安全操作
作业前准备工作要充分,检查电路、油路、水路等是否正常,戴好皮革护手腕和口罩,检查设备有无杂物。
开炼机作为重要的橡胶加工设备,其安全操作至关重要。在作业前,操作人员必须仔细检查电路、油路和水路等是否正常运行。确保电路稳定,无漏电、短路等隐患;油路畅通,为设备的各个润滑部位提供足够的润滑油;水路无堵塞,能够正常进行冷却。同时,操作人员要正确佩戴皮革护手腕和口罩,保护自身安全。此外,还需认真检查设备,确保设备内无杂物,避免在运行过程中对设备造成损坏。
正确操作设备,调整好辊距,保持平衡,避免辊筒偏载损坏设备。
在操作开炼机时,正确调整辊距是关键。辊距的调整应确保两端平衡,避免出现偏载现象。若辊距调整不当,两端大小不一,会使辊筒承受不均匀的压力,极易损坏设备。操作人员应根据生产工艺要求,精确调整辊距,确保设备稳定运行。
工作完毕,切断电源,关闭水、汽阀门。
当工作完成后,操作人员应及时切断电源,关闭水、汽阀门。切断电源可以确保设备停止运行,避免意外启动造成危险。关闭水、汽阀门可以防止水资源和能源的浪费,同时也能避免因水、汽泄漏而引发的安全事故。
注意事项
投料前检查胶料,避免混有硬的金属杂物损坏设备。
在投料前,操作人员必须对胶料进行仔细检查。若胶料中混有硬的金属杂物,投入开炼机后,会致使横压力突然加大,对设备造成严重损坏。因此,在投料前,应通过目视检查、筛选等方式,确保胶料中无金属杂物等可能损坏设备的物体。
拉推车辆和装料时注意安全,防止伤人。
在拉推车辆和进行装料操作时,操作人员要格外注意安全。拉推车辆时,应注意周围环境,防止碰撞到他人或物体,避免造成人身伤害和设备损坏。装料时,要防止偏重翻车伤人,确保物料均匀装载,避免因重心不稳而导致车辆倾覆。同时,操作人员应严格遵守操作规程,不得在设备运转部位和料盘上依靠、站坐,也不得在运转辊筒上方传送物件。
掌握辊筒预热升温速度,避免辊筒因温差过大而损坏。
辊筒预热升温速度的掌握对于开炼机的安全运行至关重要。尤其是在北方寒冷的冬季,辊筒外部与室温相一致,而辊内突然通入高温蒸汽时,内外温差可能在 120℃以上。如此大的温差会使辊筒产生巨大的应力,若再过早地加入胶料,在横压力的叠加作用下,辊筒非常容易受到破坏。为了安全起见,应当空车预热,升温速度应控制在 1~2℃/min。操作人员需严格按照这一规定进行操作,向操作人员突出强调升温速度的重要性,确保辊筒在安全的温度范围内运行。
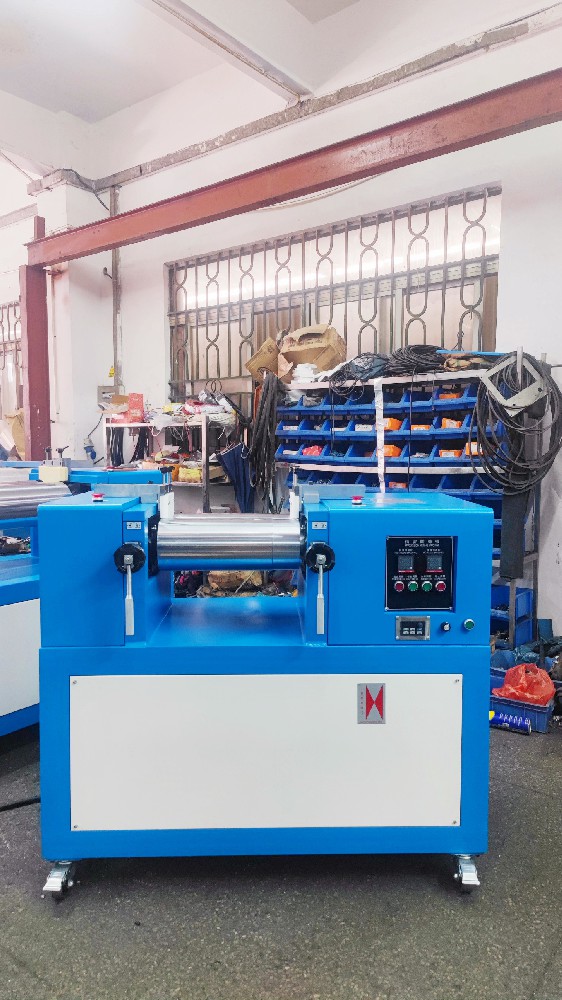